
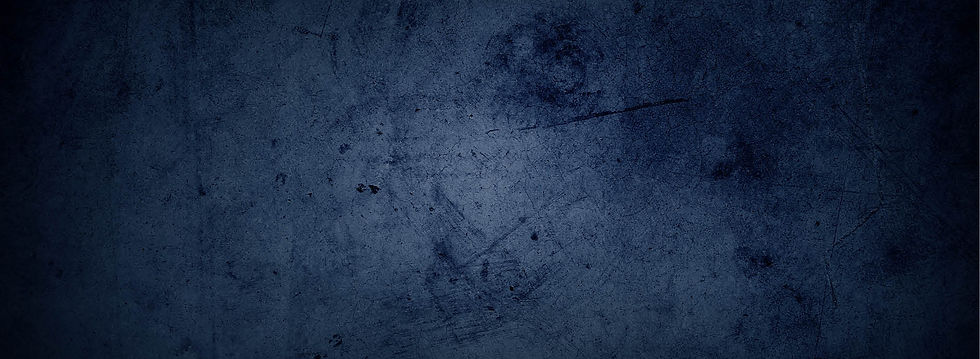
NOTHING'S AS
TOUGH AS TONY
TONY'S MANUFACTURING PROCESS
King Tony's tools are forged in-house, so he can be certain that every tool leaving his factory is made tough - just like him.
Unlike others, King Tony manufactures and distributes his own tools, so he can guarantee they will withstand the
harshest working conditions and last a lifetime.
This is what makes King Tony unique. He knows what it takes to make durable tools that stand the test of time.
He controls every step, from forge to production, to testing, to you – so you can get the best quality tools possible.
Made from strong, premium materials, each tool endures up to 15 steps in the manufacturing process.

1. Hot Forge
Precision hot forging to
mould complete fibres
improving durability
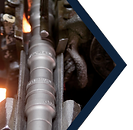
2. Grinding
Any oxide layers are ground
away and where required
tools are re-shaped to
combat any lost roundness
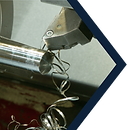
3. Lathing
Sockets are lathed to
achieve the correct outside
shape and diameter

4. Drilling
Tools that require holes
are precision drilled
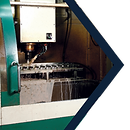
5. Machining
Tools are machined to
create their final shape
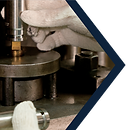
6. De-Burring
Machined tools are de-burred
removing any excess metal

7. Punching & Broaching
Spanners and similar
tools undergo punching
and broaching to achieve
accurate dimensions
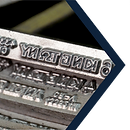
8. Marking
All King Tony tools are
marked with the
King Tony logo and
essential information

9. Heat Treatment
Tools are heat treated to
remove brittleness and
obtain the optimum
metal hardness

10. Vibrating
Tools are placed in
vibrating chambers to
remove oxide layer
and burrs caused by
heat treatment

11. Sand Blast
Tools are sand blasted to
remove any remaining, fine
oxide layers or burrs to
create a smooth finish ready
for protective plate coating

12. Plating
Tools are coated in a
nickel-chrome material to
protect them from corrosion
and to create a fresh appearance

13. Phosphate Sink
Sockets are phosphate
sunk to increase corrosion
and wear resistance

15. Rubber Strip Assembly
Where silk printing isn’t
appropriate, rubber strips are
applied. Red and blue are used
to distinguish between metric
and imperial sizes

14. Silk Printing
Where required coloured silk
printing is added to the tool.
Red and blue are used to
distinguish between metric
and imperial sizes